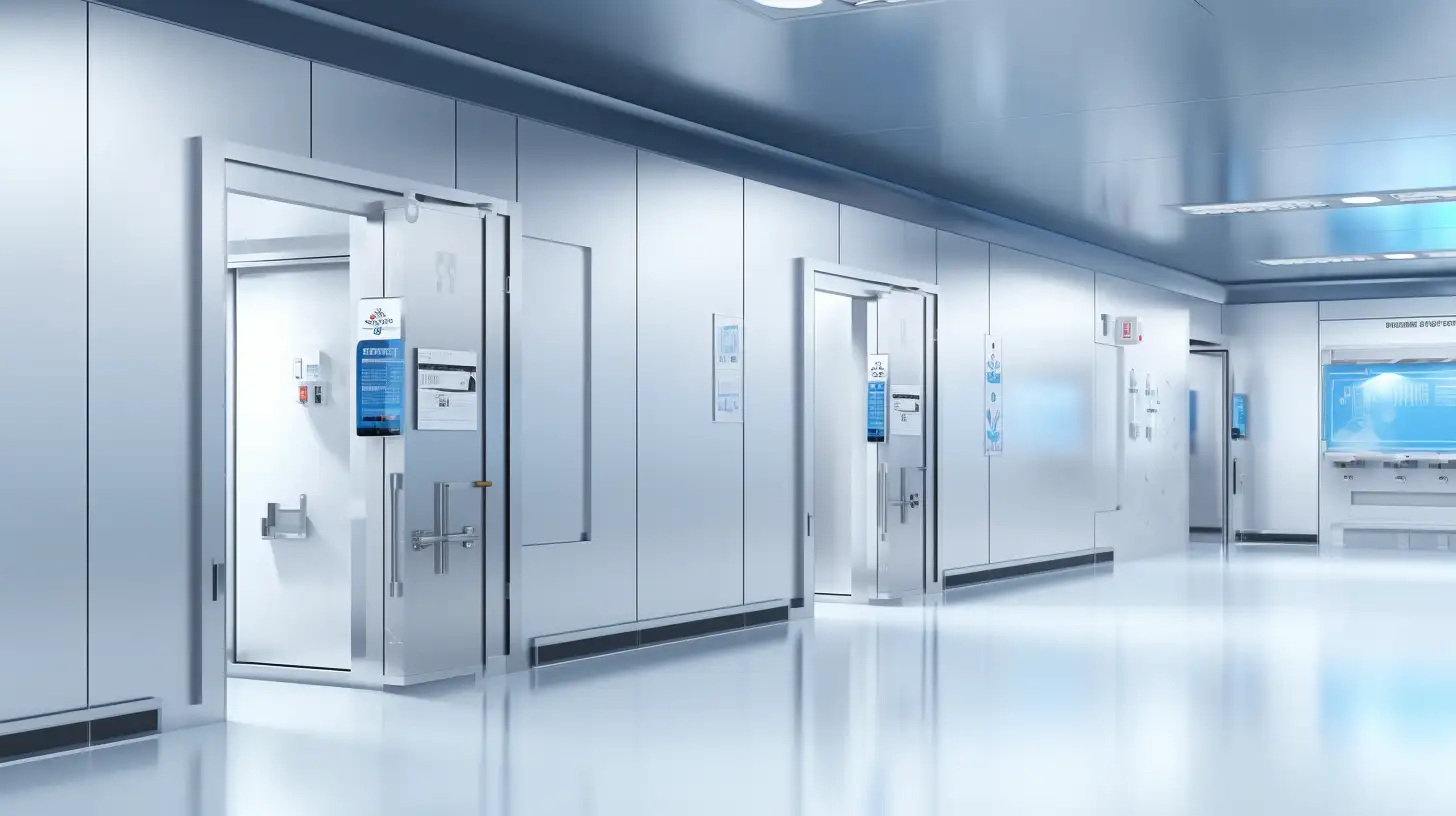
How Much Does a Walk In Cooler & Walk In Freezer Cost?
In the fast-paced world of the foodservice industry, efficient and reliable refrigeration equipment is the backbone of any successful establishment. Walk-in coolers and freezers play a crucial role in preserving the quality and freshness of perishable goods, ensuring that your customers receive top-notch products with every order. However, if you’re a business owner or foodservice manager in the market for these appliances, you might find yourself grappling with one burning question: what exactly determines walk-in freezer costs and walk-in cooler costs?
In this comprehensive guide, we will delve deep into the factors that influence the pricing of these essential refrigeration units. Whether you run a bustling restaurant, manage a commercial kitchen, or operate a foodservice establishment, this guide is tailored to provide the information you need to optimize your refrigeration investment and enhance your overall operations.
Factors Affecting Walk-In Cooler and Freezer Prices
Walk-in cooler costs and walk-in freezer costs are influenced by various factors that can significantly impact the overall price. As a business owner or foodservice manager, understanding these factors will enable you to make well-informed decisions when purchasing refrigeration equipment. Let's explore the key factors that affect the prices of walk-in coolers and freezers.
1. Size and Capacity
Walk-in cooler sizes and walk-in freezer sizes are significant determinants of their cost. Naturally, larger units with higher storage capacities will come at a higher price point. Before making a purchase, it is essential to assess your business's specific needs and estimate the volume of products you need to store. Overspending on excessive capacity can strain your budget, while an insufficiently sized unit may not accommodate your inventory adequately.
2. Insulation and Energy Efficiency
Energy efficiency and insulation play a crucial role in both the initial and long-term costs of walk-in coolers and freezers. Units with superior insulation and energy-efficient features may have a higher upfront cost, but they offer significant advantages. Energy-efficient walk-in refrigerators consume less electricity, resulting in reduced utility bills and environmental benefits. Proper insulation ensures optimal temperature retention, minimizing temperature fluctuations and food spoilage risks.
3. Cooling System and Technology
The cooling system and technology incorporated into a walk-in freezer or cooler can influence its price. Advanced cooling systems equipped with sophisticated temperature control mechanisms might have a higher initial cost. However, these modern systems provide precise temperature regulation, ensuring that your products stay fresh for an extended period. Investing in advanced technology can be beneficial in terms of maintaining the quality and safety of your stored goods.
4. Customization and Additional Features
Customization and additional features contribute to the overall cost of a walk-in cooler or freezer. While basic models are generally more affordable, businesses often require tailored solutions to meet their specific needs. Additional features such as adjustable shelving, temperature monitoring systems, and digital controls may add to the initial cost. Assess the unique requirements of your business to determine if customization is necessary and worth the investment.
Installation and Maintenance Costs of Walk-in Coolers & Freezers
Installing and maintaining walk-in coolers and freezers are crucial aspects of managing efficient and reliable refrigeration equipment. Understanding the associated costs and implementing cost-saving strategies can significantly impact your business's bottom line. In this section, we'll explore the expenses involved in walk-in cooler installation and maintenance of walk-in coolers and freezers, along with tips to maximize cost-effectiveness and achieve long-term savings.
1. Installation Costs
When budgeting for a walk-in freezer, it's essential to consider walk-in cooler installation costs. Proper installation is critical to ensuring the unit operates optimally and maintains its energy efficiency. The installation expenses can vary based on factors such as the location of the unit, accessibility of the installation site, and the complexity of the setup. It is advisable to hire experienced professionals familiar with commercial refrigeration installations to guarantee a seamless and efficient process.
2. Maintenance Costs
Regular maintenance is essential to prolong the lifespan and efficiency of your walk-in cooler or freezer. While maintenance costs are recurrent, they are essential investments to prevent major breakdowns and costly replacements in the future. Maintenance costs may include routine inspections, cleaning, and addressing any necessary repairs. Implementing a proactive maintenance plan can help detect potential issues early on, saving you money in the long run.
3. Cost-Saving Tips
To optimize cost-effectiveness, consider several strategies when purchasing and operating your walk-in cooler or freezer. First, explore reputable suppliers who offer competitive pricing on energy-efficient models. By investing in an energy-efficient unit, you can significantly reduce long-term electricity expenses. Additionally, explore preventative maintenance plans to keep your refrigeration equipment in top condition and avoid unexpected repair costs.
4. ROI and Long-Term Savings
While the upfront cost of a walk-in freezer or cooler may seem substantial, it's crucial to consider the return on investment (ROI) and long-term savings. Energy-efficient models, combined with regular maintenance, can lead to considerable savings on utility bills over time. By factoring in the potential cost savings and extended equipment lifespans, the initial investment in a high-quality walk-in cooler or freezer becomes a prudent business decision.
To Wrap Up!
Investing in a walk-in cooler or freezer is a significant decision for any foodservice establishment. Understanding the various factors that influence walk-in freezer costs and walk-in cooler costs can help you make informed choices to meet your business's unique needs. Consider the size, insulation, cooling technology, and customization of a new unit while also accounting for installation and maintenance costs. By doing so, you can ensure that your walk-in freezer or cooler enhances your business's efficiency, preserves the quality of your products, and provides long-term cost savings.
FAQ
Do walk-in coolers use a lot of electricity?
The electricity consumption of a walk-in cooler depends on factors like size, insulation, and energy efficiency. Energy-efficient models can help reduce electricity usage, resulting in cost savings over time.
How much power does a walk-in cooler use?
The power usage of a walk-in cooler varies depending on the unit's size and efficiency. On average, a walk-in cooler can consume between 5 to 15 kilowatts per day.
How should I install a walk-in cooler?
Walk-in cooler installation involves site preparation, assembly of the unit, and connection to electrical systems. It's best to hire professionals experienced in commercial refrigeration installations to ensure a seamless process.
How should a walk-in cooler be organized?
Organize your walk-in cooler by categorizing products, keeping frequently used items easily accessible, and maintaining proper airflow for uniform cooling.
How long does a walk-in cooler last?
With regular maintenance and proper care, a well-maintained walk-in cooler can last anywhere from 15 to 20 years or more, providing a considerable return on your investment.